Sealpac offers innovative packing for cheese
Sourse: The DairyNews
Whether it concerns a technical improvement of the packaging process at an artisan Swiss cheese factory, which gives its valuable skilled workers more time for cheese production, or global branding at a Portuguese cheese manufacturer that wants to significantly boost its export business, the high-tech traysealers and thermoformers from packaging specialist SEALPAC support the goals of these companies. Here are two success stories from the world of dairy.
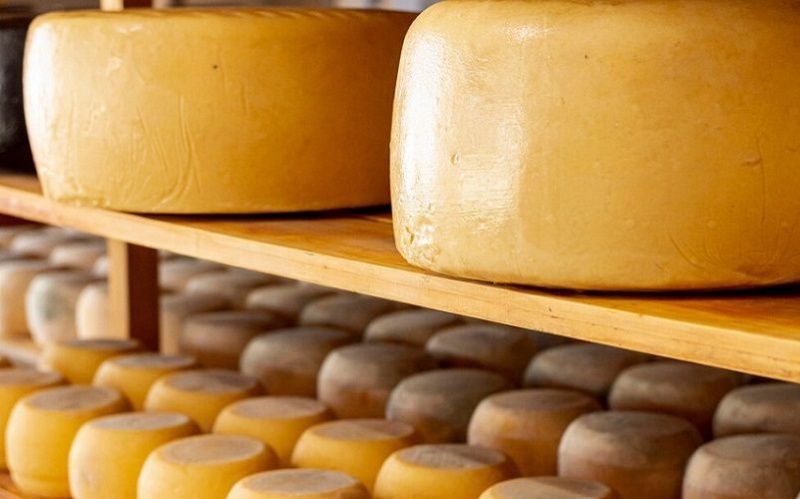
The European Union has the world's largest annual consumption of cheese. Manufacturers are competing for the hand of the consumer with their own specialty products. Regardless of whether it is a small craft company with a regional customer base or a large-scale cheese producer for export markets: to ensure the quality of cheese specialties on their way to the end user, and to offer such products in an attractive and eye-catching manner to stand out from the competition, suitable and innovative packaging is required. The solutions here are just as diverse as the product offerings on the shelves of any dairy section at retail.
A true specialist in this area is the packaging expert SEALPAC. With its renowned traysealers and thermoformers, the company has adapted to the needs of the dairy segment and offers producers innovative applications that combine optimal product protection with efficient production, as well as simplified logistics and an attractive presentation whilst using less consumables. Two examples from Switzerland and Portugal show how SEALPAC supports cheese manufacturers throughout Europe and beyond with the right packaging solutions in distributing and marketing their products.
Material-saving thermoformer packaging at artisanal Swiss company Wildberg Käserei, based in the Swiss canton of Zürich, positions itself in the luxury segment with handcrafted cheeses in around 25 different varieties. The company primarily produces in smaller quantities for local customers, including specialist retailers and delis. The products are delivered in volumes ranging from small portions to complete cheeses. Buyers are primarily consumers that value conscious nutrition, prefer handmade products, and appreciate added value over price. When the company wanted to improve product appearance by enhancing the packaging, Wildberg chose a PRO thermoformer from SEALPAC.
This compact thermoformer is tailored to small and medium-sized companies, such as Wildberg with its 16 employees, as it offers maximum flexibility and performance on a small footprint. The space-saving PRO, which uses consumables and energy extremely economically, has a modular design. The basic PRO machine is suitable to run flexible and rigid film, both for vacuum packaging and sealing only applications.
Depending on the customer’s wishes, various modules can be added to run other packaging solutions, such as MAP, skin, or shrink packaging.
CEO Roland Rüegg at Wildberg Käserei describes the improvements achieved: “Previously, we sold our cheese in pre-formed vacuum bags. The packaging did not look very professional and required a lot of plastic. We wanted a more attractive, material-saving solution and at the same time a more efficient packaging process.” With the new PRO thermoformer, the pieces of cheese are now packaged from a reel of highly transparent bottom film using Rapid Air Forming. The machine reliably manages particularly thin film that is easy to print, for example with product information, an organic label, or a brand logo. Today, various products of Wildberg Käserei are presented in an attractive and appetizing manner. The excellent peelability of the packs also offers the end consumer more convenience.
The PRO thermoformer is equipped with an innovative tooling quick exchange system, which reduces changeover times. This is perfect for the artisan cheese factory, which now produces two or three different formats every day in quick rotation on the new machine. In general, time is one of the decisive advantages for Roland Rüegg's business: “Our processes, which are still predominantly manual, have become faster thanks to the technical improvement. We used to require five people, each working four hours, to package 1,000 pieces of cheese. Now, only two employees can achieve the same amount in just one hour. Packaging has therefore become a secondary job and we can use our valuable specialist staff primarily for the cheese production.”
A true specialist in this area is the packaging expert SEALPAC. With its renowned traysealers and thermoformers, the company has adapted to the needs of the dairy segment and offers producers innovative applications that combine optimal product protection with efficient production, as well as simplified logistics and an attractive presentation whilst using less consumables. Two examples from Switzerland and Portugal show how SEALPAC supports cheese manufacturers throughout Europe and beyond with the right packaging solutions in distributing and marketing their products.
Material-saving thermoformer packaging at artisanal Swiss company Wildberg Käserei, based in the Swiss canton of Zürich, positions itself in the luxury segment with handcrafted cheeses in around 25 different varieties. The company primarily produces in smaller quantities for local customers, including specialist retailers and delis. The products are delivered in volumes ranging from small portions to complete cheeses. Buyers are primarily consumers that value conscious nutrition, prefer handmade products, and appreciate added value over price. When the company wanted to improve product appearance by enhancing the packaging, Wildberg chose a PRO thermoformer from SEALPAC.
This compact thermoformer is tailored to small and medium-sized companies, such as Wildberg with its 16 employees, as it offers maximum flexibility and performance on a small footprint. The space-saving PRO, which uses consumables and energy extremely economically, has a modular design. The basic PRO machine is suitable to run flexible and rigid film, both for vacuum packaging and sealing only applications.
Depending on the customer’s wishes, various modules can be added to run other packaging solutions, such as MAP, skin, or shrink packaging.
CEO Roland Rüegg at Wildberg Käserei describes the improvements achieved: “Previously, we sold our cheese in pre-formed vacuum bags. The packaging did not look very professional and required a lot of plastic. We wanted a more attractive, material-saving solution and at the same time a more efficient packaging process.” With the new PRO thermoformer, the pieces of cheese are now packaged from a reel of highly transparent bottom film using Rapid Air Forming. The machine reliably manages particularly thin film that is easy to print, for example with product information, an organic label, or a brand logo. Today, various products of Wildberg Käserei are presented in an attractive and appetizing manner. The excellent peelability of the packs also offers the end consumer more convenience.
The PRO thermoformer is equipped with an innovative tooling quick exchange system, which reduces changeover times. This is perfect for the artisan cheese factory, which now produces two or three different formats every day in quick rotation on the new machine. In general, time is one of the decisive advantages for Roland Rüegg's business: “Our processes, which are still predominantly manual, have become faster thanks to the technical improvement. We used to require five people, each working four hours, to package 1,000 pieces of cheese. Now, only two employees can achieve the same amount in just one hour. Packaging has therefore become a secondary job and we can use our valuable specialist staff primarily for the cheese production.”
Key News of the Week