GEA Introduces Breakthrough Technology to Revolutionize Alt Protein Production
Sourse: The DairyNews
At the Anuga FoodTec trade show in Cologne, Germany, GEA, a leading provider of engineering systems for the food, beverage, and pharmaceutical industries, is unveiling a groundbreaking innovation termed as a "technological milestone" — the perfusion platform.
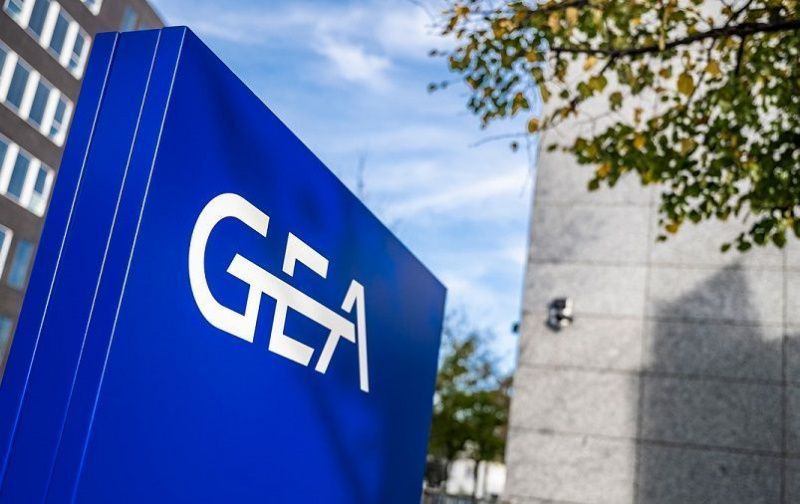
This platform, comprising the GEA Axenic-line bioreactors and the Geeky trio single-use separator, is poised to transform the landscape of cell cultivation and precision fermentation, particularly in the realm of alternative protein production. By enhancing productivity and cost efficiency, the technology aims to bridge the price gap between conventional and alternative foods.
Tatjana Krampitz, Head of New Food Technology Management at GEA, highlights the significance of perfusion technology, stating, “We see perfusion as one of the most promising technologies because it cuts the production cost of alternative proteins on several fronts.” The process involves separating cells fr om depleted nutrient solutions and reintroducing them into the bioreactor with fresh medium under sterile conditions. This facilitates the removal of growth-inhibiting metabolites, enhancing productivity, cell density, and ensuring consistent product quality — a crucial factor for regulatory approval.
Furthermore, the ability to reprocess media significantly reduces production costs, thereby making alternative protein products more accessible to consumers. GEA's single-use separator plays a pivotal role in pilot processes, enabling startups to validate their product ideas without the need for complex cleaning and sterilization facilities.
Krampitz emphasizes the importance of reliable pilot plants for startups, stating, “What the market currently needs are reliable pilot plants that are quick to set up and meet industrial standards. Our single-use separators enable start-ups in particular to work under sterile conditions, which helps them surmount a major challenge.”
Perfusion technology also offers benefits for upstream and downstream processes by enabling continuous operation of bioreactors and improving capacity utilization. GEA experts estimate that perfusion could reduce bioreactor size, media, and space requirements by 10%, ultimately driving down production costs.
Krampitz envisions a future wh ere perfusion technology revolutionizes bioreactor design and production processes, stating, “Perfusion lets us grow cells in a much smaller space. In the long term, this technology will blaze a trail when it comes to shrinking bioreactors and hence reducing both the quantity of stainless steel needed and the nutrient and cleaning media required.”
Tatjana Krampitz, Head of New Food Technology Management at GEA, highlights the significance of perfusion technology, stating, “We see perfusion as one of the most promising technologies because it cuts the production cost of alternative proteins on several fronts.” The process involves separating cells fr om depleted nutrient solutions and reintroducing them into the bioreactor with fresh medium under sterile conditions. This facilitates the removal of growth-inhibiting metabolites, enhancing productivity, cell density, and ensuring consistent product quality — a crucial factor for regulatory approval.
Furthermore, the ability to reprocess media significantly reduces production costs, thereby making alternative protein products more accessible to consumers. GEA's single-use separator plays a pivotal role in pilot processes, enabling startups to validate their product ideas without the need for complex cleaning and sterilization facilities.
Krampitz emphasizes the importance of reliable pilot plants for startups, stating, “What the market currently needs are reliable pilot plants that are quick to set up and meet industrial standards. Our single-use separators enable start-ups in particular to work under sterile conditions, which helps them surmount a major challenge.”
Perfusion technology also offers benefits for upstream and downstream processes by enabling continuous operation of bioreactors and improving capacity utilization. GEA experts estimate that perfusion could reduce bioreactor size, media, and space requirements by 10%, ultimately driving down production costs.
Krampitz envisions a future wh ere perfusion technology revolutionizes bioreactor design and production processes, stating, “Perfusion lets us grow cells in a much smaller space. In the long term, this technology will blaze a trail when it comes to shrinking bioreactors and hence reducing both the quantity of stainless steel needed and the nutrient and cleaning media required.”
Key News of the Week