The History of Innovation and Technological Development in China's Dairy Industry
Source: The DairyNews
Technological innovation has played an extremely important role in the development of China’s dairy industry. Over the 75 years since the founding of the People's Republic of China, the dairy industry has continuously overcome challenges of different eras through technological advancements:
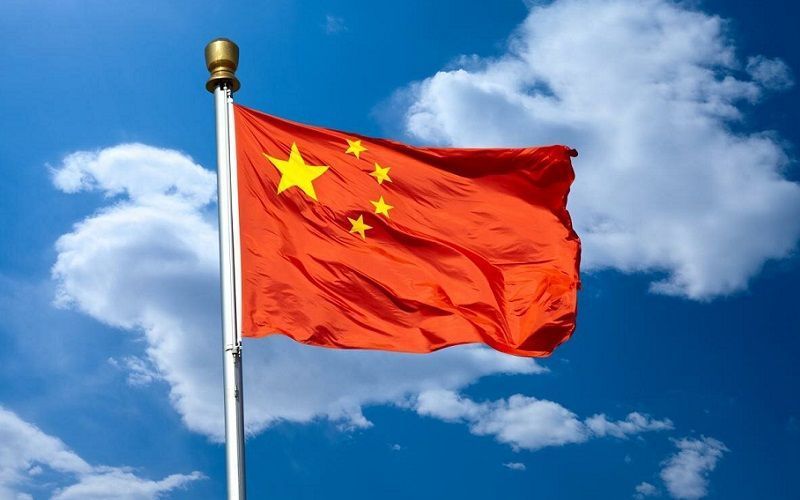
1949-1978, Production Technology Germination Period: The mechanization of milking, milk delivery, and milk storage laid the foundation for large-scale development.
1979-2007, High-Speed Mechanization Development Period: The application of sterilization technology and continuous filling released the huge growth potential of the dairy industry.
2008-2017, Modern Dairy Structure Adjustment Period: Intelligentization pushed China's dairy production enterprises to reach the world's advanced level.
2018 to Present, High-Quality Development Leap Period: As the Chinese dairy industry faces cyclical challenges once again, is technological innovation still the ultimate answer?
"One pound of milk a day makes the Chinese strong." Many people are familiar with this slogan proposed in 2006. In fact, the nutritional value of milk has long been widely recognized worldwide. In the 1930s, the United States launched the "Three Cups of Milk Campaign." In the 1960s, Japan initiated the "A Cup of Milk Makes a Nation Strong" campaign. Since the 1970s, India has implemented the "Operation Flood" program. It can be seen that the widespread advocacy of milk consumption and the rapid development of the dairy industry in China came later than in many developed countries.
Although starting late, the Chinese dairy industry has developed rapidly, benefiting fr om China's fast economic development and large population base, with penetration rates increasing quickly. In terms of production, milk output was only 200,000 tonnes in 1949, but it reached 41.97 million tonnes in 2023, growing by about 210 times. The output of dairy products increased from 624 tonnes in 1952 to 30.546 million tonnes in 2023, an increase of nearly 49,000 times, with dairy product consumption continuing to rise, becoming the fastest-growing product in livestock consumption. In terms of production methods, China has made significant progress from traditional "manual milking" agriculture to modern assembly line production, to the organic era emphasizing "completely natural" and "pollution-free" processes, and now to the intelligent era of digital production.
Regarding the significant progress in the development of the dairy industry since the founding of New China, Wang Caiyun, a national representative, senior expert at the National Dairy Technology Innovation Center, and research director at the Yili Group Global Innovation Center, pointed out at this year's Two Sessions that the rapid development of China's dairy industry, with steady improvements in production, quality, and equipment levels, is inseparable from the power of "technological innovation." Looking back at the development history of China's dairy processing, the power of technological innovation has been indispensable, prompting continuous industry changes and bringing milk into thousands of households.
1949-1978: Production Technology Germination Period
In the early stages of the new China, the dairy industry was in its infancy, constrained by limited technology and management levels, with a weak foundation and slow development. Today, we are accustomed to using "thousands of heads" and "thousands of tonnes" to count cattle inventory and milk processing volume. However, in the early days of the People's Republic, many cities could only describe them in terms of "a few heads" and "a few tonnes." According to "The History of China's Dairy Industry," dairy processing in the early days of the People's Republic was mainly concentrated in some traditional dairy production enterprises and rural family workshops. Due to the lack of modern production equipment and technical support, product quality was inconsistent, production efficiency was low, and market competitiveness was weak. At that time, only a few dairy factories in eastern cities, such as the Nanjing Weigang Dairy Farm and the Wenzhou Baihao Dairy Factory, had a small amount of dairy machinery, while most small dairy factories used simple "local equipment." Domestic dairy production was very low, with only 624 tonnes of dairy products nationwide in 1952, and the product structure was simple, mainly milk powder, condensed milk, and a small amount of cheese. According to the 1952 Shanghai Dairy Industry Annual Report, the city's 131 milk production enterprises had a daily milk output of 24,985.2 kg (excluding state-owned farms). The main equipment included 28 boilers, 158 motors, 27 sterilizers, 28 refrigerating machines, 20 bottling machines, and other machinery (including cream separators, supercooling tanks, vacuum pumps, and storage tanks).
The starting point of China's dairy development can be traced back to 1953. With the start of the First Five-Year Plan, agricultural cooperation and public-private partnerships were promoted nationwide, and a series of economic reforms were carried out, with small-scale state-owned dairy farms being established in various regions. By the end of the First Five-Year Plan in 1957, the national dairy product output reached 13,000 tonnes, with an average annual growth rate of 83.5% compared to 1949. At this time, the level of dairy processing equipment, technology, and capacity also improved, with over 70 large and small dairy enterprises nationwide, mainly producing milk powder, including 12 with spray drying equipment, 14 with drum drying equipment, and 44 with flat pan drying equipment.
At that time, the supply of milk in large and medium-sized cities nationwide was generally tight, and milk powder was still considered a "special need." In 1958, a letter from the public expressed the hope of solving the problem of children's milk consumption. Subsequently, the nation mobilized to develop dairy production. Despite the impact of the "Three Years of Difficulties" period, the dairy industry gradually developed and recovered. Dairy production quality was closely related to processing technology and management levels. To ensure strict quality control of dairy production, in 1974, the Beijing Planning Commission arranged for the mass production of 100 electronic pulse milking machines, replacing manual milking with machine milking on state-owned farms. Later, the Beijing Municipal Government arranged for the manufacture of 8 milk tank trucks to achieve mechanized transport of raw milk. In 1974, the Beijing Agriculture and Forestry Bureau submitted a request to the municipal government to purchase Japanese paper-packaging fresh milk machines, marking the first proposal to use advanced foreign milk packaging machinery. The request document pointed out that the Japanese milk packaging machine was compact, required less factory space, was easy to disinfect with air, fully automated, and economically efficient. It reduced labor operations such as washing bottles, caps, and filling, and cut transportation volume by more than half. Purchasing advanced milk packaging machinery could improve packaging efficiency and quality, gradually realizing modern milk packaging.
The early mechanization of each stage, including milking, milk delivery, and storage, initiated a wave of technical transformation, laying a solid foundation for the gradual transition of the dairy industry toward scale, modernization, and marketization.
1979-2007: High-Speed Mechanization Development Period
Since 1978, China's liquid milk industry has seen broad development opportunities, with continuous improvements in technology and management levels and gradual optimization of industrial structure. In dairy processing, the government encouraged and supported the development of the industry, establishing dairy enterprises across the country and introducing advanced sterilized milk production technology and equipment. In the early stages of reform and opening up, due to technological limitations, dairy products were mainly milk powder and pasteurized milk for short-distance transportation and small-scale distribution. Starting in the 1980s, the technical equipment level of Chinese dairy factories significantly improved. The introduction of advanced foreign equipment brought dairy processing to the world's advanced level, marking the beginning of the era of mechanized and large-scale production.
According to the "China Dairy Industry" magazine, in 1984, the Zalute Banner Dairy Factory in Inner Mongolia introduced a sheet-type ultra-high-temperature sterilizer and an aseptic filling machine from Sweden's Alfa-Laval company, marking the first complete introduction of sterilized milk production equipment in China. In 1986, the Shanghai Dairy No. 6 Factory on Chongming Island introduced ultra-high-temperature instant sterilization (UHT) technology and equipment from Tetra Pak, installing a "Tetra Brik" sterilized milk filling production line and implementing on-site training to improve employee skills. In 1987, the Urumqi Farm Management Bureau in Xinjiang introduced an electric-heated UHT milk production line from Finland. In December 1989, Sweden's Alfa-Laval company held a packaging technology seminar in China. The introduction of equipment and learning of technology promoted the widespread use of dairy processing technology in China, significantly enhancing the overall equipment level and independent innovation capacity of the dairy processing industry, narrowing the gap with developed dairy countries.
UHT sterilized milk is filled into aseptic packaging in a sterile environment. This packaging material, composed of paper, aluminum, and plastic, effectively blocks air, moisture, and light, extending the shelf life of milk without the need for a cold chain, allowing milk to be sold nationwide. Consequently, the market no longer only circulated low-temperature dairy products, and the penetration rate of ambient dairy products rapidly increased. The advent of ambient sterilized milk expanded the growth space of the dairy industry, promoting processing efficiency, reducing production costs, and laying a solid foundation for sustainable development.
In terms of overall processing efficiency, in the early 1990s, the largest dairy enterprise in China processed 200 tonnes of raw milk per day, reaching 1,200 tonnes after entering the 21st century. By 2008, the annual raw milk processing capacity of the largest dairy enterprise had reached 3.845 million tonnes, a significant leap in processing capacity. As for individual enterprises, during the latter stages of the "Tenth Five-Year Plan," a batch of large dairy factories was completed and put into operation. For example, in 2005, Yili's Jinchuan New Industrial Park installed 18 UHT milk production lines, making it the largest liquid milk production plant in Asia at the time. That same year, Mengniu Dairy's Baoji Industrial Park began construction, installing 25 liquid milk production lines with an annual output of 250,000 tonnes. In 2006, Tianjin Bright Dairy & Food Co., Ltd. completed and put into production an advanced liquid milk production line, introducing Tetra Pak's TBA22 filling machine, the highest-speed filling machine at the time, capable of filling 20,000 packages per hour.
At this point, China's dairy processing industry had undergone tremendous changes in terms of production capacity, scale, equipment, and product structure. Some dairy enterprises turned to group operations through asset restructuring and mergers, continuously expanding concentration and scale. By the end of 2007, China's dairy product output reached 17.87 million tonnes, including 14.41 million tonnes of liquid milk and over 3 million tonnes of dry dairy products. There were over 700 processing enterprises above a designated size, with a total industrial output value of 134.881 billion yuan, creating a number of key leading enterprises such as Mengniu, Yili, Bright Dairy, Sanyuan, and Wandashan.
Technological innovation has played an extremely important role in the development process of the dairy industry. Through technological innovation, dairy enterprises have improved product quality and taste, enhanced product competitiveness, and adjusted product structure. This is mainly reflected in several aspects: First, the overall increase in liquid milk production. The production and sales growth of liquid milk were significantly higher than the overall dairy products, especially in large and medium-sized cities, wh ere liquid milk consumption became mainstream, with an average annual growth rate of 17.92% in liquid milk consumption from 1992 to 2006. Second, among liquid milk products, the growth rate of ambient sterilized milk was the fastest. In 2000, China launched the "National Student Drinking Milk Program," stipulating that student drinking milk products should be ultra-high-temperature sterilized and aseptically packaged, with designated enterprises required to have a daily raw milk processing capacity of at least 50 tonnes, greatly promoting the development of sterilized milk. In 2001, the total amount of sterilized milk surpassed pasteurized milk for the first time. Third, the proportion of liquid milk consumption gradually increased, from only 50% of total dairy products in 1995 to 81% in 2007. According to the China Dairy Industry Association, in 2007, the output of liquid milk from enterprises above a designated size was 14.41 million tonnes, including 12% pasteurized milk, 71% UHT milk, and 17% fermented milk.
2008-2017: Modern Dairy Structure Adjustment Period
After entering the 21st century, China had basically met the conditions for building a modern dairy industry. However, during the 2008-2017 period, the dairy industry experienced many challenges and opportunities, including the significant impact of the infant formula scandal. The increased consumer demand for dairy product quality and safety, coupled with intensified market competition, motivated enterprises to increase technological investments, transform dairy production methods, and improve product quality to meet market demand. Additionally, this period required stricter regulation and management of dairy product safety and quality by both the government and enterprises.
According to Song Kungang, Honorary Chairman of the China National Committee of the International Dairy Federation, since 2008, dairy and infant formula enterprises have undergone extensive technological upgrades and industrial enhancements. All enterprises' technical equipment levels, testing capabilities, scientific research capacities, quality assurance abilities, and professional workforce levels have significantly improved, with production processes achieving programmed management and reaching the level of "intelligent factories." Dairy and infant formula enterprises have implemented ISO and HACCP management systems, with raw materials entering and products leaving the factory strictly inspected according to regulations. This ensures traceability of raw material sources, accountability for product quality, and tracking of product destinations. Today, the technical equipment level, testing capabilities, scientific research capacities, and management levels of China's dairy enterprises are on par with world standards.
This illustrates that technological innovation continuously drives the transformation and upgrading of the liquid milk and dairy product industries. In 2008, the national dairy product output was 18.11 million tonnes, including 15.25 million tonnes of liquid milk. In 2017, the national dairy product output reached 29.35 million tonnes, a 62.1% increase, including 26.917 million tonnes of liquid milk, a 76.5% increase. According to the China Dairy Industry Association's 2015 statistics, the composition of liquid milk products nationwide was approximately 8.0% pasteurized milk, 41.0% UHT milk, 28.5% modulated milk, and 22.5% fermented milk. Among these, fermented milk saw the fastest growth, with a compound annual growth rate of 20% from 2010 to 2015.
During this period, technological innovation in dairy processing exhibited several characteristics: First, digital development enabled dairy enterprises to achieve complete automation and traceability in production planning, equipment management, quality control, cost management, energy management, and logistics management, breaking down information barriers. Second, intelligent development entered a substantive stage with the advent of new information technologies such as the Internet of Things and big data intelligence. Dairy processing plants' intelligent transformation enabled comprehensive control of production processes, improving production management efficiency through more refined production coordination and planning. Third, green development addressed increasing concerns about environmental protection in an era of growing energy and environmental issues. Many companies along the industrial chain adopted green industry development as their direction, promoting sustainable processing and packaging solutions for the food and beverage industry to reduce costs, increase efficiency, save energy, and reduce emissions.
2018 to Present: High-Quality Development Leap Period
The 19th National Congress of the Communist Party of China first proposed "high-quality development." In 2018, the State Council's General Office issued the "Opinions on Promoting Dairy Industry Revitalization and Ensuring Dairy Product Quality and Safety," emphasizing the need to continuously improve the quality, efficiency, and competitiveness of dairy development, vigorously promote the modernization of the dairy industry, and strengthen the national dairy industry. Guided by high-quality development, the performance of China's raw milk production, dairy processing, import and export, product quality, market marketing, and economic benefits has been outstanding compared to historical levels. National awareness of the nutritional value of dairy products has further improved, marking a steady development period for the dairy industry.
Relevant data shows that China's dairy product output reached 30.546 million tonnes in 2023, an increase of 3.1% year-on-year. The global recognition of Chinese dairy brands has significantly improved, with Yili and Mengniu continuing to rank among the top 10 global dairy companies, and several dairy companies' products winning awards in international dairy quality competitions. The market now offers a wide range of products, including various flavored yogurts, UHT milk, lactose-free milk, infant formula, adult formulated milk powder, and cheese, greatly enriching consumers' diets. During the COVID-19 pandemic, consumers' focus on healthy eating increased, making milk a staple product along with grain, meat, and vegetables, further solidifying the market position of dairy products, especially liquid milk.
However, in recent years, the liquid milk market has faced challenges such as declining consumption and narrowed profit margins due to negative population growth and the impact of the pandemic. Despite the growth in disposable income since 2022, weakened expectations of the economic environment have affected consumer enthusiasm, with spending primarily meeting rigid demand, reducing consumption of products with greater elasticity. The per capita dairy consumption in 2023 was approximately 41.3 kg, a 1.5% decrease year-on-year. Liquid milk consumption showed a slight downward trend, with a year-on-year sales growth rate of -1.5% in 2023, and the Ministry of Agriculture and Rural Affairs' Food and Nutrition Development Research Institute monitoring offline liquid milk sales showing an overall decline, with consumption down 3.7% year-on-year.
In this context, it is challenging for a single industry to change external factors such as population decline and weakened economic expectations. Therefore, companies need to respond swiftly to uncertainties, continuously promote industrial transformation and upgrading through technological innovation, and enhance competitiveness by reducing costs, increasing efficiency, and promoting green development.
In 2024, the development of new quality productivity points out breakthroughs, development space, and opportunities for the entire industry. The development of new quality productivity is not a partial optimization or simple iteration of traditional productivity but requires more efficient and environmentally friendly production methods to enhance industry competitiveness, necessitating disruptive technological innovation. For the dairy processing industry, technological innovation-driven new quality productivity development can help reduce costs, improve efficiency, enhance product competitiveness, stimulate dairy consumption, address current challenges in dairy development, and promote high-quality industry development.
For example, Yili Group has empowered all its factories nationwide through digital intelligence, significantly enhancing productivity and doubling production efficiency. In 2022, Yili Modern Smart Health Valley aimed to build a global intelligent manufacturing benchmark base for liquid milk, introducing highly automated and intelligent liquid milk filling production lines that nearly doubled production line efficiency, shortened product innovation cycles by 20%, and improved indirect procurement efficiency by 40%, maintaining a 5%-7% cost advantage compared to the industry. On May 28, 2023, Mengniu completed and put into production its first fully digital intelligent factory in Ningxia, aiming to achieve the highest annual labor efficiency in the global dairy industry, with 100 employees creating an annual output of 1 million tonnes and an annual output value of 10 billion yuan, improving labor productivity nearly 20 times compared to traditional factories, while overall energy consumption decreased by 43%. Tianrun Dairy adheres to a refined management model, continuously enhancing factory capacity through technological transformation and optimization. At the end of 2023, the company announced plans to raise funds for new factory construction and equip intelligent production equipment to further improve dairy, especially ambient dairy production levels, and expand product sales regions.
Dairy packaging suppliers have also contributed to the development of new quality productivity in the dairy industry. Suppliers like Tetra Pak have accelerated global scientific research breakthroughs and focused their innovative results on the Chinese market. For example, Tetra Pak's E3 high-speed filling machine, launched in China in March 2024, is the first to apply electron beam sterilization technology in the packaging field. This disruptive technological innovation makes the E3 high-speed filling machine a global leader in production efficiency and environmental benefits, capable of filling up to 40,000 packages per hour, increasing annual unit area production capacity by more than 60% compared to the previous A3 model, setting a global record. Additionally, replacing traditional hydrogen peroxide sterilization with electron beam technology can save up to 45% water and 30% electricity, reducing environmental impact. The E3 high-speed filling machine has already been applied in the factories of two leading Chinese dairy companies, becoming an indispensable part of accelerating digital intelligence and sustainable development transformation.
Technological innovation is the key driving force during the high-quality development period of the dairy industry. The proposal of new quality productivity provides scientific guidance for exploring new fields and tracks of dairy development and shaping new growth drivers and advantages, pointing the way for high-quality dairy development. By tackling key core technologies, promoting revolutionary technological breakthroughs, and innovatively allocating production factors, the industry can accelerate the construction of a modern industrial system.
The history of the liquid milk processing industry in China includes significant moments from "nothing" to "something," from "few" to "many," and from "weak" to "strong." In this historical development, technological innovation has played a crucial role in every stage of China's dairy industry, becoming a key factor driving continuous progress in liquid milk processing. Overall, after years of development, China's liquid milk industry has made significant progress. With the continuous advancement of technological innovation and changing market demands, the industry is expected to have an even brighter future, providing high-quality, safe dairy products to the public. Technological innovation will continue to lead China's liquid milk industry towards a more brilliant future.
Original text author in Chinese: 新乳业
1979-2007, High-Speed Mechanization Development Period: The application of sterilization technology and continuous filling released the huge growth potential of the dairy industry.
2008-2017, Modern Dairy Structure Adjustment Period: Intelligentization pushed China's dairy production enterprises to reach the world's advanced level.
2018 to Present, High-Quality Development Leap Period: As the Chinese dairy industry faces cyclical challenges once again, is technological innovation still the ultimate answer?
"One pound of milk a day makes the Chinese strong." Many people are familiar with this slogan proposed in 2006. In fact, the nutritional value of milk has long been widely recognized worldwide. In the 1930s, the United States launched the "Three Cups of Milk Campaign." In the 1960s, Japan initiated the "A Cup of Milk Makes a Nation Strong" campaign. Since the 1970s, India has implemented the "Operation Flood" program. It can be seen that the widespread advocacy of milk consumption and the rapid development of the dairy industry in China came later than in many developed countries.
Although starting late, the Chinese dairy industry has developed rapidly, benefiting fr om China's fast economic development and large population base, with penetration rates increasing quickly. In terms of production, milk output was only 200,000 tonnes in 1949, but it reached 41.97 million tonnes in 2023, growing by about 210 times. The output of dairy products increased from 624 tonnes in 1952 to 30.546 million tonnes in 2023, an increase of nearly 49,000 times, with dairy product consumption continuing to rise, becoming the fastest-growing product in livestock consumption. In terms of production methods, China has made significant progress from traditional "manual milking" agriculture to modern assembly line production, to the organic era emphasizing "completely natural" and "pollution-free" processes, and now to the intelligent era of digital production.
Regarding the significant progress in the development of the dairy industry since the founding of New China, Wang Caiyun, a national representative, senior expert at the National Dairy Technology Innovation Center, and research director at the Yili Group Global Innovation Center, pointed out at this year's Two Sessions that the rapid development of China's dairy industry, with steady improvements in production, quality, and equipment levels, is inseparable from the power of "technological innovation." Looking back at the development history of China's dairy processing, the power of technological innovation has been indispensable, prompting continuous industry changes and bringing milk into thousands of households.
1949-1978: Production Technology Germination Period
In the early stages of the new China, the dairy industry was in its infancy, constrained by limited technology and management levels, with a weak foundation and slow development. Today, we are accustomed to using "thousands of heads" and "thousands of tonnes" to count cattle inventory and milk processing volume. However, in the early days of the People's Republic, many cities could only describe them in terms of "a few heads" and "a few tonnes." According to "The History of China's Dairy Industry," dairy processing in the early days of the People's Republic was mainly concentrated in some traditional dairy production enterprises and rural family workshops. Due to the lack of modern production equipment and technical support, product quality was inconsistent, production efficiency was low, and market competitiveness was weak. At that time, only a few dairy factories in eastern cities, such as the Nanjing Weigang Dairy Farm and the Wenzhou Baihao Dairy Factory, had a small amount of dairy machinery, while most small dairy factories used simple "local equipment." Domestic dairy production was very low, with only 624 tonnes of dairy products nationwide in 1952, and the product structure was simple, mainly milk powder, condensed milk, and a small amount of cheese. According to the 1952 Shanghai Dairy Industry Annual Report, the city's 131 milk production enterprises had a daily milk output of 24,985.2 kg (excluding state-owned farms). The main equipment included 28 boilers, 158 motors, 27 sterilizers, 28 refrigerating machines, 20 bottling machines, and other machinery (including cream separators, supercooling tanks, vacuum pumps, and storage tanks).
The starting point of China's dairy development can be traced back to 1953. With the start of the First Five-Year Plan, agricultural cooperation and public-private partnerships were promoted nationwide, and a series of economic reforms were carried out, with small-scale state-owned dairy farms being established in various regions. By the end of the First Five-Year Plan in 1957, the national dairy product output reached 13,000 tonnes, with an average annual growth rate of 83.5% compared to 1949. At this time, the level of dairy processing equipment, technology, and capacity also improved, with over 70 large and small dairy enterprises nationwide, mainly producing milk powder, including 12 with spray drying equipment, 14 with drum drying equipment, and 44 with flat pan drying equipment.
At that time, the supply of milk in large and medium-sized cities nationwide was generally tight, and milk powder was still considered a "special need." In 1958, a letter from the public expressed the hope of solving the problem of children's milk consumption. Subsequently, the nation mobilized to develop dairy production. Despite the impact of the "Three Years of Difficulties" period, the dairy industry gradually developed and recovered. Dairy production quality was closely related to processing technology and management levels. To ensure strict quality control of dairy production, in 1974, the Beijing Planning Commission arranged for the mass production of 100 electronic pulse milking machines, replacing manual milking with machine milking on state-owned farms. Later, the Beijing Municipal Government arranged for the manufacture of 8 milk tank trucks to achieve mechanized transport of raw milk. In 1974, the Beijing Agriculture and Forestry Bureau submitted a request to the municipal government to purchase Japanese paper-packaging fresh milk machines, marking the first proposal to use advanced foreign milk packaging machinery. The request document pointed out that the Japanese milk packaging machine was compact, required less factory space, was easy to disinfect with air, fully automated, and economically efficient. It reduced labor operations such as washing bottles, caps, and filling, and cut transportation volume by more than half. Purchasing advanced milk packaging machinery could improve packaging efficiency and quality, gradually realizing modern milk packaging.
The early mechanization of each stage, including milking, milk delivery, and storage, initiated a wave of technical transformation, laying a solid foundation for the gradual transition of the dairy industry toward scale, modernization, and marketization.
1979-2007: High-Speed Mechanization Development Period
Since 1978, China's liquid milk industry has seen broad development opportunities, with continuous improvements in technology and management levels and gradual optimization of industrial structure. In dairy processing, the government encouraged and supported the development of the industry, establishing dairy enterprises across the country and introducing advanced sterilized milk production technology and equipment. In the early stages of reform and opening up, due to technological limitations, dairy products were mainly milk powder and pasteurized milk for short-distance transportation and small-scale distribution. Starting in the 1980s, the technical equipment level of Chinese dairy factories significantly improved. The introduction of advanced foreign equipment brought dairy processing to the world's advanced level, marking the beginning of the era of mechanized and large-scale production.
According to the "China Dairy Industry" magazine, in 1984, the Zalute Banner Dairy Factory in Inner Mongolia introduced a sheet-type ultra-high-temperature sterilizer and an aseptic filling machine from Sweden's Alfa-Laval company, marking the first complete introduction of sterilized milk production equipment in China. In 1986, the Shanghai Dairy No. 6 Factory on Chongming Island introduced ultra-high-temperature instant sterilization (UHT) technology and equipment from Tetra Pak, installing a "Tetra Brik" sterilized milk filling production line and implementing on-site training to improve employee skills. In 1987, the Urumqi Farm Management Bureau in Xinjiang introduced an electric-heated UHT milk production line from Finland. In December 1989, Sweden's Alfa-Laval company held a packaging technology seminar in China. The introduction of equipment and learning of technology promoted the widespread use of dairy processing technology in China, significantly enhancing the overall equipment level and independent innovation capacity of the dairy processing industry, narrowing the gap with developed dairy countries.
UHT sterilized milk is filled into aseptic packaging in a sterile environment. This packaging material, composed of paper, aluminum, and plastic, effectively blocks air, moisture, and light, extending the shelf life of milk without the need for a cold chain, allowing milk to be sold nationwide. Consequently, the market no longer only circulated low-temperature dairy products, and the penetration rate of ambient dairy products rapidly increased. The advent of ambient sterilized milk expanded the growth space of the dairy industry, promoting processing efficiency, reducing production costs, and laying a solid foundation for sustainable development.
In terms of overall processing efficiency, in the early 1990s, the largest dairy enterprise in China processed 200 tonnes of raw milk per day, reaching 1,200 tonnes after entering the 21st century. By 2008, the annual raw milk processing capacity of the largest dairy enterprise had reached 3.845 million tonnes, a significant leap in processing capacity. As for individual enterprises, during the latter stages of the "Tenth Five-Year Plan," a batch of large dairy factories was completed and put into operation. For example, in 2005, Yili's Jinchuan New Industrial Park installed 18 UHT milk production lines, making it the largest liquid milk production plant in Asia at the time. That same year, Mengniu Dairy's Baoji Industrial Park began construction, installing 25 liquid milk production lines with an annual output of 250,000 tonnes. In 2006, Tianjin Bright Dairy & Food Co., Ltd. completed and put into production an advanced liquid milk production line, introducing Tetra Pak's TBA22 filling machine, the highest-speed filling machine at the time, capable of filling 20,000 packages per hour.
At this point, China's dairy processing industry had undergone tremendous changes in terms of production capacity, scale, equipment, and product structure. Some dairy enterprises turned to group operations through asset restructuring and mergers, continuously expanding concentration and scale. By the end of 2007, China's dairy product output reached 17.87 million tonnes, including 14.41 million tonnes of liquid milk and over 3 million tonnes of dry dairy products. There were over 700 processing enterprises above a designated size, with a total industrial output value of 134.881 billion yuan, creating a number of key leading enterprises such as Mengniu, Yili, Bright Dairy, Sanyuan, and Wandashan.
Technological innovation has played an extremely important role in the development process of the dairy industry. Through technological innovation, dairy enterprises have improved product quality and taste, enhanced product competitiveness, and adjusted product structure. This is mainly reflected in several aspects: First, the overall increase in liquid milk production. The production and sales growth of liquid milk were significantly higher than the overall dairy products, especially in large and medium-sized cities, wh ere liquid milk consumption became mainstream, with an average annual growth rate of 17.92% in liquid milk consumption from 1992 to 2006. Second, among liquid milk products, the growth rate of ambient sterilized milk was the fastest. In 2000, China launched the "National Student Drinking Milk Program," stipulating that student drinking milk products should be ultra-high-temperature sterilized and aseptically packaged, with designated enterprises required to have a daily raw milk processing capacity of at least 50 tonnes, greatly promoting the development of sterilized milk. In 2001, the total amount of sterilized milk surpassed pasteurized milk for the first time. Third, the proportion of liquid milk consumption gradually increased, from only 50% of total dairy products in 1995 to 81% in 2007. According to the China Dairy Industry Association, in 2007, the output of liquid milk from enterprises above a designated size was 14.41 million tonnes, including 12% pasteurized milk, 71% UHT milk, and 17% fermented milk.
2008-2017: Modern Dairy Structure Adjustment Period
After entering the 21st century, China had basically met the conditions for building a modern dairy industry. However, during the 2008-2017 period, the dairy industry experienced many challenges and opportunities, including the significant impact of the infant formula scandal. The increased consumer demand for dairy product quality and safety, coupled with intensified market competition, motivated enterprises to increase technological investments, transform dairy production methods, and improve product quality to meet market demand. Additionally, this period required stricter regulation and management of dairy product safety and quality by both the government and enterprises.
According to Song Kungang, Honorary Chairman of the China National Committee of the International Dairy Federation, since 2008, dairy and infant formula enterprises have undergone extensive technological upgrades and industrial enhancements. All enterprises' technical equipment levels, testing capabilities, scientific research capacities, quality assurance abilities, and professional workforce levels have significantly improved, with production processes achieving programmed management and reaching the level of "intelligent factories." Dairy and infant formula enterprises have implemented ISO and HACCP management systems, with raw materials entering and products leaving the factory strictly inspected according to regulations. This ensures traceability of raw material sources, accountability for product quality, and tracking of product destinations. Today, the technical equipment level, testing capabilities, scientific research capacities, and management levels of China's dairy enterprises are on par with world standards.
This illustrates that technological innovation continuously drives the transformation and upgrading of the liquid milk and dairy product industries. In 2008, the national dairy product output was 18.11 million tonnes, including 15.25 million tonnes of liquid milk. In 2017, the national dairy product output reached 29.35 million tonnes, a 62.1% increase, including 26.917 million tonnes of liquid milk, a 76.5% increase. According to the China Dairy Industry Association's 2015 statistics, the composition of liquid milk products nationwide was approximately 8.0% pasteurized milk, 41.0% UHT milk, 28.5% modulated milk, and 22.5% fermented milk. Among these, fermented milk saw the fastest growth, with a compound annual growth rate of 20% from 2010 to 2015.
During this period, technological innovation in dairy processing exhibited several characteristics: First, digital development enabled dairy enterprises to achieve complete automation and traceability in production planning, equipment management, quality control, cost management, energy management, and logistics management, breaking down information barriers. Second, intelligent development entered a substantive stage with the advent of new information technologies such as the Internet of Things and big data intelligence. Dairy processing plants' intelligent transformation enabled comprehensive control of production processes, improving production management efficiency through more refined production coordination and planning. Third, green development addressed increasing concerns about environmental protection in an era of growing energy and environmental issues. Many companies along the industrial chain adopted green industry development as their direction, promoting sustainable processing and packaging solutions for the food and beverage industry to reduce costs, increase efficiency, save energy, and reduce emissions.
2018 to Present: High-Quality Development Leap Period
The 19th National Congress of the Communist Party of China first proposed "high-quality development." In 2018, the State Council's General Office issued the "Opinions on Promoting Dairy Industry Revitalization and Ensuring Dairy Product Quality and Safety," emphasizing the need to continuously improve the quality, efficiency, and competitiveness of dairy development, vigorously promote the modernization of the dairy industry, and strengthen the national dairy industry. Guided by high-quality development, the performance of China's raw milk production, dairy processing, import and export, product quality, market marketing, and economic benefits has been outstanding compared to historical levels. National awareness of the nutritional value of dairy products has further improved, marking a steady development period for the dairy industry.
Relevant data shows that China's dairy product output reached 30.546 million tonnes in 2023, an increase of 3.1% year-on-year. The global recognition of Chinese dairy brands has significantly improved, with Yili and Mengniu continuing to rank among the top 10 global dairy companies, and several dairy companies' products winning awards in international dairy quality competitions. The market now offers a wide range of products, including various flavored yogurts, UHT milk, lactose-free milk, infant formula, adult formulated milk powder, and cheese, greatly enriching consumers' diets. During the COVID-19 pandemic, consumers' focus on healthy eating increased, making milk a staple product along with grain, meat, and vegetables, further solidifying the market position of dairy products, especially liquid milk.
However, in recent years, the liquid milk market has faced challenges such as declining consumption and narrowed profit margins due to negative population growth and the impact of the pandemic. Despite the growth in disposable income since 2022, weakened expectations of the economic environment have affected consumer enthusiasm, with spending primarily meeting rigid demand, reducing consumption of products with greater elasticity. The per capita dairy consumption in 2023 was approximately 41.3 kg, a 1.5% decrease year-on-year. Liquid milk consumption showed a slight downward trend, with a year-on-year sales growth rate of -1.5% in 2023, and the Ministry of Agriculture and Rural Affairs' Food and Nutrition Development Research Institute monitoring offline liquid milk sales showing an overall decline, with consumption down 3.7% year-on-year.
In this context, it is challenging for a single industry to change external factors such as population decline and weakened economic expectations. Therefore, companies need to respond swiftly to uncertainties, continuously promote industrial transformation and upgrading through technological innovation, and enhance competitiveness by reducing costs, increasing efficiency, and promoting green development.
In 2024, the development of new quality productivity points out breakthroughs, development space, and opportunities for the entire industry. The development of new quality productivity is not a partial optimization or simple iteration of traditional productivity but requires more efficient and environmentally friendly production methods to enhance industry competitiveness, necessitating disruptive technological innovation. For the dairy processing industry, technological innovation-driven new quality productivity development can help reduce costs, improve efficiency, enhance product competitiveness, stimulate dairy consumption, address current challenges in dairy development, and promote high-quality industry development.
For example, Yili Group has empowered all its factories nationwide through digital intelligence, significantly enhancing productivity and doubling production efficiency. In 2022, Yili Modern Smart Health Valley aimed to build a global intelligent manufacturing benchmark base for liquid milk, introducing highly automated and intelligent liquid milk filling production lines that nearly doubled production line efficiency, shortened product innovation cycles by 20%, and improved indirect procurement efficiency by 40%, maintaining a 5%-7% cost advantage compared to the industry. On May 28, 2023, Mengniu completed and put into production its first fully digital intelligent factory in Ningxia, aiming to achieve the highest annual labor efficiency in the global dairy industry, with 100 employees creating an annual output of 1 million tonnes and an annual output value of 10 billion yuan, improving labor productivity nearly 20 times compared to traditional factories, while overall energy consumption decreased by 43%. Tianrun Dairy adheres to a refined management model, continuously enhancing factory capacity through technological transformation and optimization. At the end of 2023, the company announced plans to raise funds for new factory construction and equip intelligent production equipment to further improve dairy, especially ambient dairy production levels, and expand product sales regions.
Dairy packaging suppliers have also contributed to the development of new quality productivity in the dairy industry. Suppliers like Tetra Pak have accelerated global scientific research breakthroughs and focused their innovative results on the Chinese market. For example, Tetra Pak's E3 high-speed filling machine, launched in China in March 2024, is the first to apply electron beam sterilization technology in the packaging field. This disruptive technological innovation makes the E3 high-speed filling machine a global leader in production efficiency and environmental benefits, capable of filling up to 40,000 packages per hour, increasing annual unit area production capacity by more than 60% compared to the previous A3 model, setting a global record. Additionally, replacing traditional hydrogen peroxide sterilization with electron beam technology can save up to 45% water and 30% electricity, reducing environmental impact. The E3 high-speed filling machine has already been applied in the factories of two leading Chinese dairy companies, becoming an indispensable part of accelerating digital intelligence and sustainable development transformation.
Technological innovation is the key driving force during the high-quality development period of the dairy industry. The proposal of new quality productivity provides scientific guidance for exploring new fields and tracks of dairy development and shaping new growth drivers and advantages, pointing the way for high-quality dairy development. By tackling key core technologies, promoting revolutionary technological breakthroughs, and innovatively allocating production factors, the industry can accelerate the construction of a modern industrial system.
The history of the liquid milk processing industry in China includes significant moments from "nothing" to "something," from "few" to "many," and from "weak" to "strong." In this historical development, technological innovation has played a crucial role in every stage of China's dairy industry, becoming a key factor driving continuous progress in liquid milk processing. Overall, after years of development, China's liquid milk industry has made significant progress. With the continuous advancement of technological innovation and changing market demands, the industry is expected to have an even brighter future, providing high-quality, safe dairy products to the public. Technological innovation will continue to lead China's liquid milk industry towards a more brilliant future.
Original text author in Chinese: 新乳业