Kerry Foods Enhances Sustainability and Reduces Costs with Veolia Water Technologies Effluent Treatment Solution
Source: DairyNews.today
Veolia Water Technologies has successfully optimized the effluent treatment process at Kerry Foods' butter and cream production facility in Ossett, West Yorkshire, resulting in substantial cost savings and a reduced environmental footprint. By switching to a plant-based coagulant, the site has halved its sludge volume, eliminating the need for costly weekly sludge collection and significantly lowering its carbon footprint.
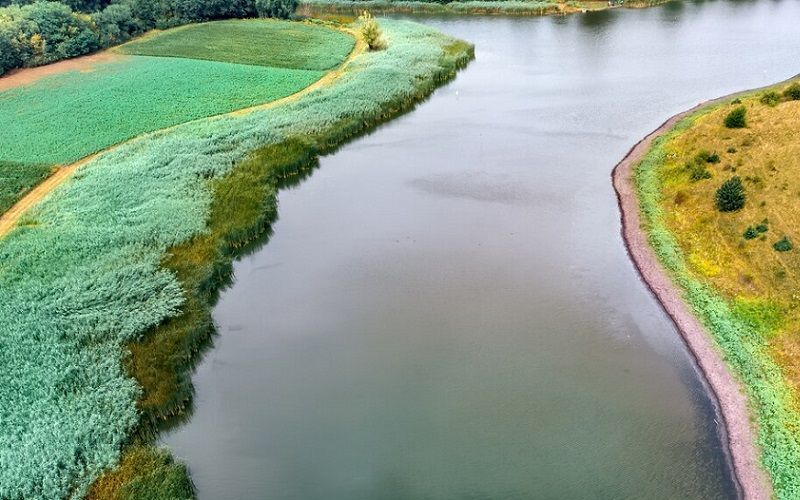
he Kerry Foods facility, which processes butter and cream, previously used a dissolved air flotation (DAF) unit with metal-based coagulants. The team, led by Engineering Maintenance Manager Owen Millar, sought to improve the efficiency and sustainability of the plant's effluent treatment. Veolia Water Technologies, leveraging its existing relationship with Kerry Foods, proposed the use of its HYDREX® 62925 plant-based coagulant to optimize the DAF system.
Following extensive testing, the new solution reduced the sludge volume by 50%, cutting the facility's annual sludge removal costs of £50,000. Additionally, the more concentrated sludge produced by the new process has a 50% higher calorific value, making it suitable for sale as Anaerobic Digestor (AD) feed, generating potential revenue for Kerry Foods.
Beyond cost savings, the change has also led to significant environmental benefits. Transport movements associated with sludge collection have been reduced by approximately 75%, contributing to a lower carbon footprint. Replacing metal-based coagulants with the plant-based HYDREX® 62925 further enhanced sustainability by reducing chemical usage and improving safety for operators.
Millar praised Veolia's support throughout the process: "The team provided expert assistance and allowed us ample time to run trials and make informed decisions," he said. The transition was also facilitated by Veolia’s training for operators, ensuring smooth implementation and addressing any initial issues promptly.
With these improvements, Kerry Foods has not only reduced operational costs but also bolstered its environmental credentials, making it an example of how sustainable practices can deliver both economic and ecological benefits in the food processing industry.
Following extensive testing, the new solution reduced the sludge volume by 50%, cutting the facility's annual sludge removal costs of £50,000. Additionally, the more concentrated sludge produced by the new process has a 50% higher calorific value, making it suitable for sale as Anaerobic Digestor (AD) feed, generating potential revenue for Kerry Foods.
Beyond cost savings, the change has also led to significant environmental benefits. Transport movements associated with sludge collection have been reduced by approximately 75%, contributing to a lower carbon footprint. Replacing metal-based coagulants with the plant-based HYDREX® 62925 further enhanced sustainability by reducing chemical usage and improving safety for operators.
Millar praised Veolia's support throughout the process: "The team provided expert assistance and allowed us ample time to run trials and make informed decisions," he said. The transition was also facilitated by Veolia’s training for operators, ensuring smooth implementation and addressing any initial issues promptly.
With these improvements, Kerry Foods has not only reduced operational costs but also bolstered its environmental credentials, making it an example of how sustainable practices can deliver both economic and ecological benefits in the food processing industry.