DeLaval is supplying equipment for dairy farm in China, which will become the new world leader in the number of robots
Source: eldala.kz
This year, DeLaval is currently supporting our customer to build what is planned to be the largest AMS (Automatic Milking System) farm in the world, starting with 50 DeLaval VMS V300 in 2024. Victor Stefan, Business Development Manager at DeLaval in Kazakhstan and Kyrgyzstan, told what benefits the robot milker provides.
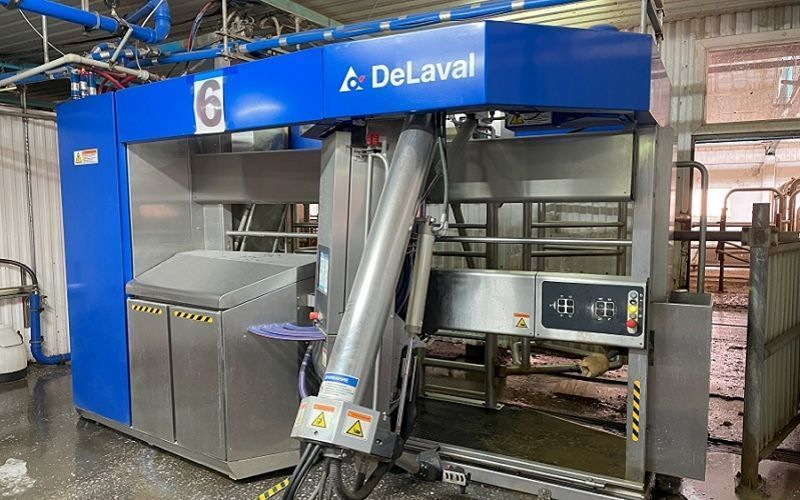
Robotic milking is actively conquering the segment of medium and large dairy farms today.
The growth rate of robotics in Western Europe has recently been plus 10-12% per year. The leaders here are Holland, Denmark, and Germany. The widespread introduction of robots in these markets was initially due to the fact that manual labor is very expensive. In addition, the convenience for installing robots is created by the fact that farms are mostly small.
"If the average farm in Sweden is 40-60 heads, then hiring two milkers is 4-5 thousand euros per month," explained Viktor Stefan. - Such a business will not justify itself. Therefore, the farmer needs to either milk the cows himself, with his own hands, or install a robot milker. And the first robots were produced just with the calculation of the load of 40-50 heads per day."
Today, robot milkers have become more productive, the commercial load per one is around 65 cows, in some cases up to 80 cows per day. This is related to farm operations, cow condition and cannot be replicated across all farms. More and more large scale robotic farms are planned and built in the past 10 years.
"In the last 10 years, the technology of robotic milking has been increasingly being implemented on large farms," said Viktor Stefan. - We know examples when farms have been successfully operating in the milking parlor for 15-20 years, but due to the rising cost of skilled labor, they switched to robotic milking. In Germany, one of the largest farms with a population of 1,100 milking herds last year began the transition from a carousel to robotic milking. Last year we visited it, and we saw that the carousel is still working, but gradually they are transferring more and more animals to milking by robots. In the USA, more and more farms for 1000-2000 heads are equipped with robots."
The largest robotic farm today is located in Chile, about 60 robots are installed there, 3.5 thousand cows are milked.
As for Kazakhstan, the first robotic dairy complex appeared in the country in 2012 near Ust-Kamenogorsk, on the Bobrovka+ farm (part of the Vostok-Moloko corporation). The dairy kit at the Bobrovka + farm has been working successfully all these years, and this season the investor started building another robotic farm in East Kazakhstan region, as he appreciated all the advantages of robotic technology for keeping and milking cows. The partner of both projects is DeLaval, which was one of the first companies in the world to develop and manufacture milking robots.
One of the main tasks that DeLaval faces is the development of an optimal technological solution for each specific farm for the choice of milking equipment, says Victor Stefan. The expert sees long-term prospects in this regard in the gradual transition of farms from traditional milking methods to the use of milking robots. At the moment, a small number of ITFs in Kazakhstan are equipped with such equipment, but over time progress will do its job, and the country will gradually join the global trend of robotization. And it consists in reducing manual labor and introducing modern technological solutions.
"There are three ways to milk a cow on a farm," said Victor Stefan. - If we go from basic to more innovative, then the first is milking into a milk pipeline with tethered cows. This technology has been around for over 100 years and is gradually becoming obsolete, as it involves a large proportion of manual labor. Hence the low labor productivity: the load on one operator is about 40-50 heads. The second method is loose maintenance with milking in milking parlors. There is also a lot of manual labor here, but productivity is already higher. The load on the operator is on average 100-200 heads in stationary milking parlors of the parallel or herringbone type, and up to 400 heads in milking parlors of the carousel type. The third way is to use robot milkers. It is an advanced technology with a minimum of manual labor and high productivity. When using this milking technology, one operator can serve up to 500-600 heads per shift (depending on the size of the barn)."
According to the expert, one operator per shift is enough to service eight robots (this is a milking herd about 600 heads). A robot is the best way to manage a herd today, as it allows you to collect much more information about an animal than a traditional milking parlor. Robot analyzes the quality of milk from each share separately. This allows you to identify mastitis in the early stages, carry out treatment on time and avoid economic losses. The quality of milk is also improved due to the fact that the robot can release milk from the diseased lobe into a separate container or completely prohibit milking of the diseased nipple. This eliminates the ingress of milk with high somatics, blood or antibiotics into the general tank. A processor who buys consistently high-quality milk from a farm is willing to pay more for it.
It is estimated that the volume of milk yields on robotic farms is also higher than on traditional farms due to all the above-mentioned factors (stress reduction, in-depth health monitoring, early diagnosis of problems, targeted feeding).
“We believe robotic technology will help the industry become more productive and sustainable. ”Said Vicktor Stefan.
The growth rate of robotics in Western Europe has recently been plus 10-12% per year. The leaders here are Holland, Denmark, and Germany. The widespread introduction of robots in these markets was initially due to the fact that manual labor is very expensive. In addition, the convenience for installing robots is created by the fact that farms are mostly small.
"If the average farm in Sweden is 40-60 heads, then hiring two milkers is 4-5 thousand euros per month," explained Viktor Stefan. - Such a business will not justify itself. Therefore, the farmer needs to either milk the cows himself, with his own hands, or install a robot milker. And the first robots were produced just with the calculation of the load of 40-50 heads per day."
Today, robot milkers have become more productive, the commercial load per one is around 65 cows, in some cases up to 80 cows per day. This is related to farm operations, cow condition and cannot be replicated across all farms. More and more large scale robotic farms are planned and built in the past 10 years.
"In the last 10 years, the technology of robotic milking has been increasingly being implemented on large farms," said Viktor Stefan. - We know examples when farms have been successfully operating in the milking parlor for 15-20 years, but due to the rising cost of skilled labor, they switched to robotic milking. In Germany, one of the largest farms with a population of 1,100 milking herds last year began the transition from a carousel to robotic milking. Last year we visited it, and we saw that the carousel is still working, but gradually they are transferring more and more animals to milking by robots. In the USA, more and more farms for 1000-2000 heads are equipped with robots."
The largest robotic farm today is located in Chile, about 60 robots are installed there, 3.5 thousand cows are milked.
As for Kazakhstan, the first robotic dairy complex appeared in the country in 2012 near Ust-Kamenogorsk, on the Bobrovka+ farm (part of the Vostok-Moloko corporation). The dairy kit at the Bobrovka + farm has been working successfully all these years, and this season the investor started building another robotic farm in East Kazakhstan region, as he appreciated all the advantages of robotic technology for keeping and milking cows. The partner of both projects is DeLaval, which was one of the first companies in the world to develop and manufacture milking robots.
One of the main tasks that DeLaval faces is the development of an optimal technological solution for each specific farm for the choice of milking equipment, says Victor Stefan. The expert sees long-term prospects in this regard in the gradual transition of farms from traditional milking methods to the use of milking robots. At the moment, a small number of ITFs in Kazakhstan are equipped with such equipment, but over time progress will do its job, and the country will gradually join the global trend of robotization. And it consists in reducing manual labor and introducing modern technological solutions.
"There are three ways to milk a cow on a farm," said Victor Stefan. - If we go from basic to more innovative, then the first is milking into a milk pipeline with tethered cows. This technology has been around for over 100 years and is gradually becoming obsolete, as it involves a large proportion of manual labor. Hence the low labor productivity: the load on one operator is about 40-50 heads. The second method is loose maintenance with milking in milking parlors. There is also a lot of manual labor here, but productivity is already higher. The load on the operator is on average 100-200 heads in stationary milking parlors of the parallel or herringbone type, and up to 400 heads in milking parlors of the carousel type. The third way is to use robot milkers. It is an advanced technology with a minimum of manual labor and high productivity. When using this milking technology, one operator can serve up to 500-600 heads per shift (depending on the size of the barn)."
According to the expert, one operator per shift is enough to service eight robots (this is a milking herd about 600 heads). A robot is the best way to manage a herd today, as it allows you to collect much more information about an animal than a traditional milking parlor. Robot analyzes the quality of milk from each share separately. This allows you to identify mastitis in the early stages, carry out treatment on time and avoid economic losses. The quality of milk is also improved due to the fact that the robot can release milk from the diseased lobe into a separate container or completely prohibit milking of the diseased nipple. This eliminates the ingress of milk with high somatics, blood or antibiotics into the general tank. A processor who buys consistently high-quality milk from a farm is willing to pay more for it.
It is estimated that the volume of milk yields on robotic farms is also higher than on traditional farms due to all the above-mentioned factors (stress reduction, in-depth health monitoring, early diagnosis of problems, targeted feeding).
“We believe robotic technology will help the industry become more productive and sustainable. ”Said Vicktor Stefan.
Key News of the Week